Understanding Auto Parts Mould: A Deep Dive into the Industry
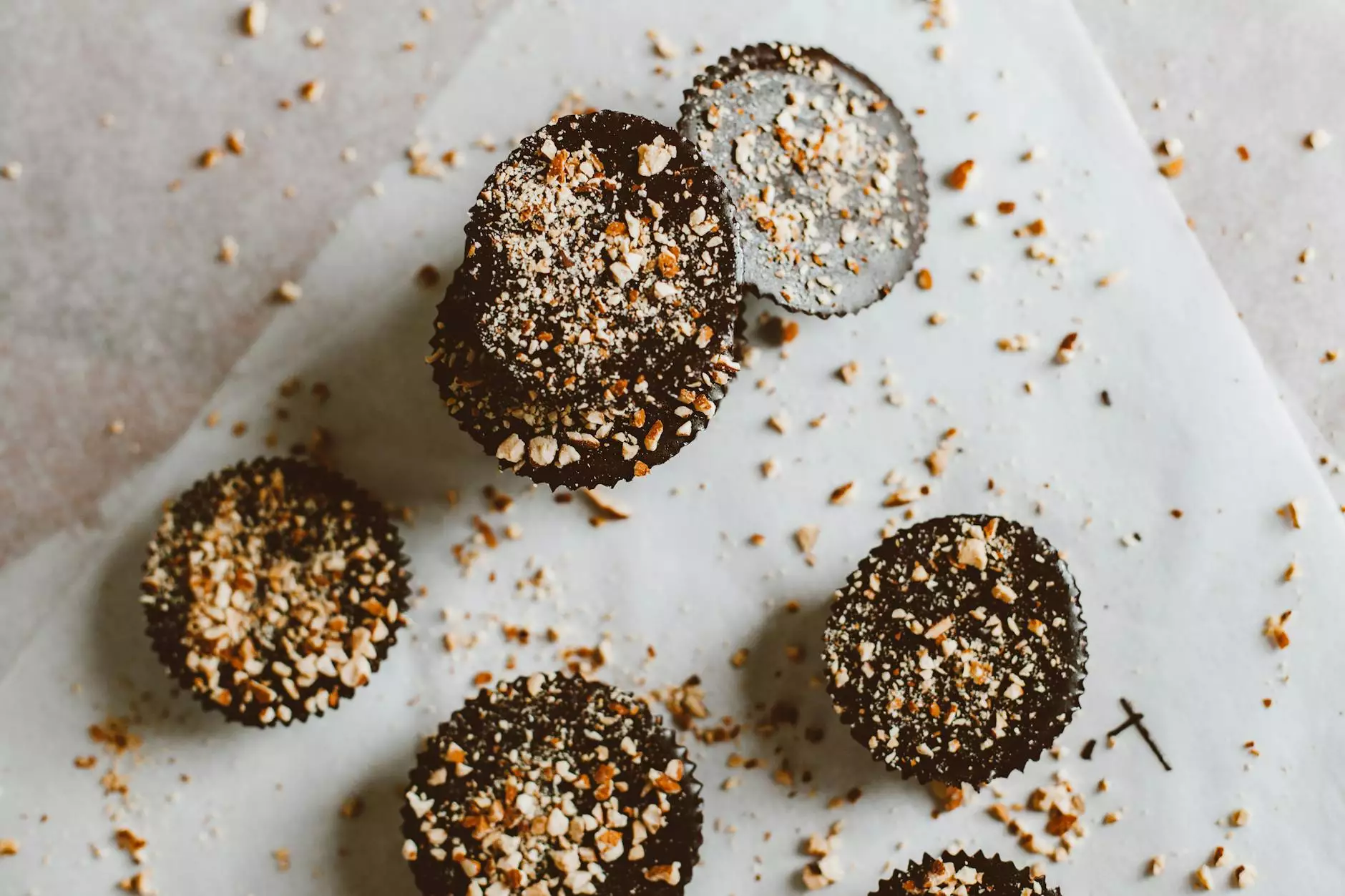
Auto parts mould plays a crucial role in the automotive manufacturing process. It serves as the blueprint for creating high-quality auto components, ensuring precision, durability, and scalability in production. As the automotive industry evolves, so too does the technology and techniques involved in mould making. In this article, we will explore the intricate details of auto parts mould, its significance, the materials used, and how businesses like Deep Mould leverage modern techniques to deliver exceptional products.
The Importance of Auto Parts Mould in Manufacturing
In the automotive industry, the demand for precision-engineered components is paramount. The quality of these components often hinges on the effectiveness of the mould used during manufacturing. Here are some reasons why auto parts mould is essential:
- Precision Engineering: Auto parts moulds are designed to meet exact specifications, which leads to higher accuracy in the final product.
- Mass Production: With advanced moulding techniques, manufacturers can produce thousands of parts quickly and efficiently.
- Cost Efficiency: High-quality moulds reduce waste and errors, resulting in lower production costs in the long run.
- Durability: Moulds are crafted to withstand high temperatures and pressures, ensuring longevity in the production process.
Types of Moulds Used in Auto Parts Manufacturing
There are various types of moulds employed in the production of auto parts. Each serves a specific purpose and offers unique advantages:
1. Injection Moulds
Injection moulding is one of the most common methods for creating auto parts. It involves injecting molten material into a pre-designed mould. Key benefits include:
- Ability to create complex shapes.
- High production speed.
- Consistent quality across batches.
2. Blow Moulds
Blow moulding is primarily used for making hollow components like fuel tanks and various fluid containers. The advantages of blow moulds include:
- Efficient use of materials.
- Versatile in size and shape options.
- Lightweight products that maintain structural integrity.
3. Compression Moulds
Compression moulding is often used for rubber and composite materials in auto components, such as seals and gaskets. The benefits include:
- Cost-effective for low-volume production.
- Suitable for large, heavy components.
- Minimal waste of materials.
Materials Used in Auto Parts Mould
The choice of material for auto parts mould is critical, as it directly affects the quality and durability of the final product. Common materials include:
1. Steel
Steel is widely used for mould making due to its strength and longevity. It can endure high pressures and temperatures, making it ideal for complex and demanding applications.
2. Aluminum
Aluminum is lightweight and offers excellent thermal conductivity. It is often used for smaller production runs where speed is essential. However, aluminum moulds may not last as long as steel moulds, especially in high-volume situations.
3. High-Density Polyethylene (HDPE)
For specific applications, especially in blow moulding, HDPE is used due to its flexibility and resistance to impact. This material is particularly beneficial in creating lightweight auto components.
The Role of Metal Fabricators in Mould Production
Metal fabricators play a vital role in the creation of auto parts moulds. Their expertise ensures that the moulds are expertly crafted to meet the high standards required in the automotive industry. Here’s how metal fabricators contribute:
1. Precision Machining
Metal fabricators utilize precision machining techniques to create precise mould components. This involves the use of CNC (Computer Numerical Control) machines that ensure exact measurements and designs.
2. Quality Control
Quality control is critical in manufacturing. Metal fabricators implement rigorous testing procedures to ensure that the moulds meet industry specifications and are capable of producing high-quality parts.
3. Customization
Each automotive application may require a unique mould design. Metal fabricators can customize moulds to fit specific requirements, allowing for flexibility in production depending on the client's needs.
Innovations in Auto Parts Mould Technology
As the automotive industry continues to grow and change, so too does the technology surrounding auto parts mould. Innovative techniques are being developed to enhance efficiency and reduce costs:
1. 3D Printing in Mould Making
3D printing is revolutionizing the way moulds are produced. It allows for rapid prototyping of mould designs, which can significantly shorten the overall production timeline. This technology enables manufacturers to test and adjust designs before committing to full-scale production.
2. Advanced Materials
The development of new materials that can withstand greater temperatures and pressures is enhancing the durability of moulds. These advancements allow for longer-lasting moulds, reducing the frequency of replacements.
3. Automation and Robotics
The incorporation of automation and robotics in the mould production process improves efficiency and accuracy. Automated systems can consistently deliver parts to exact specifications, minimizing human error.
Choosing the Right Partner for Auto Parts Mould Production
When it comes to selecting a company for auto parts mould production, it's essential to consider several factors:
1. Experience and Reputation
Companies like Deep Mould boast years of experience in the industry, which is crucial for navigating the complexities of mould production. A strong reputation can often indicate reliability and expertise.
2. Technological Capabilities
Ensure that the company utilizes the latest technology and techniques in their mould production process. Companies that invest in advanced machinery and innovative techniques are more likely to provide superior products.
3. Customization Options
Every automotive component is unique. The ideal partner should be able to offer customization in mould design to meet your specific needs, ensuring the final product aligns perfectly with your requirements.
Conclusion: The Future of Auto Parts Mould
The future of auto parts mould is bright, with continuous advancements in technology and materials driving the industry forward. Businesses must stay abreast of these changes to remain competitive. As the demand for high-quality components rises, so will the need for sophisticated mould solutions. By partnering with experienced and technologically advanced metal fabricators like Deep Mould, manufacturers can ensure that they meet the highest standards of quality, efficiency, and customization in their production processes.
Call to Action
If you are in the automotive industry and need reliable and high-quality auto parts mould, consider reaching out to industry leaders like Deep Mould. Their expertise in metal fabrication and dedication to quality assurance makes them an ideal partner for your mould production needs.