Understanding Auto Injection Molding: Revolutionizing Metal Fabrication
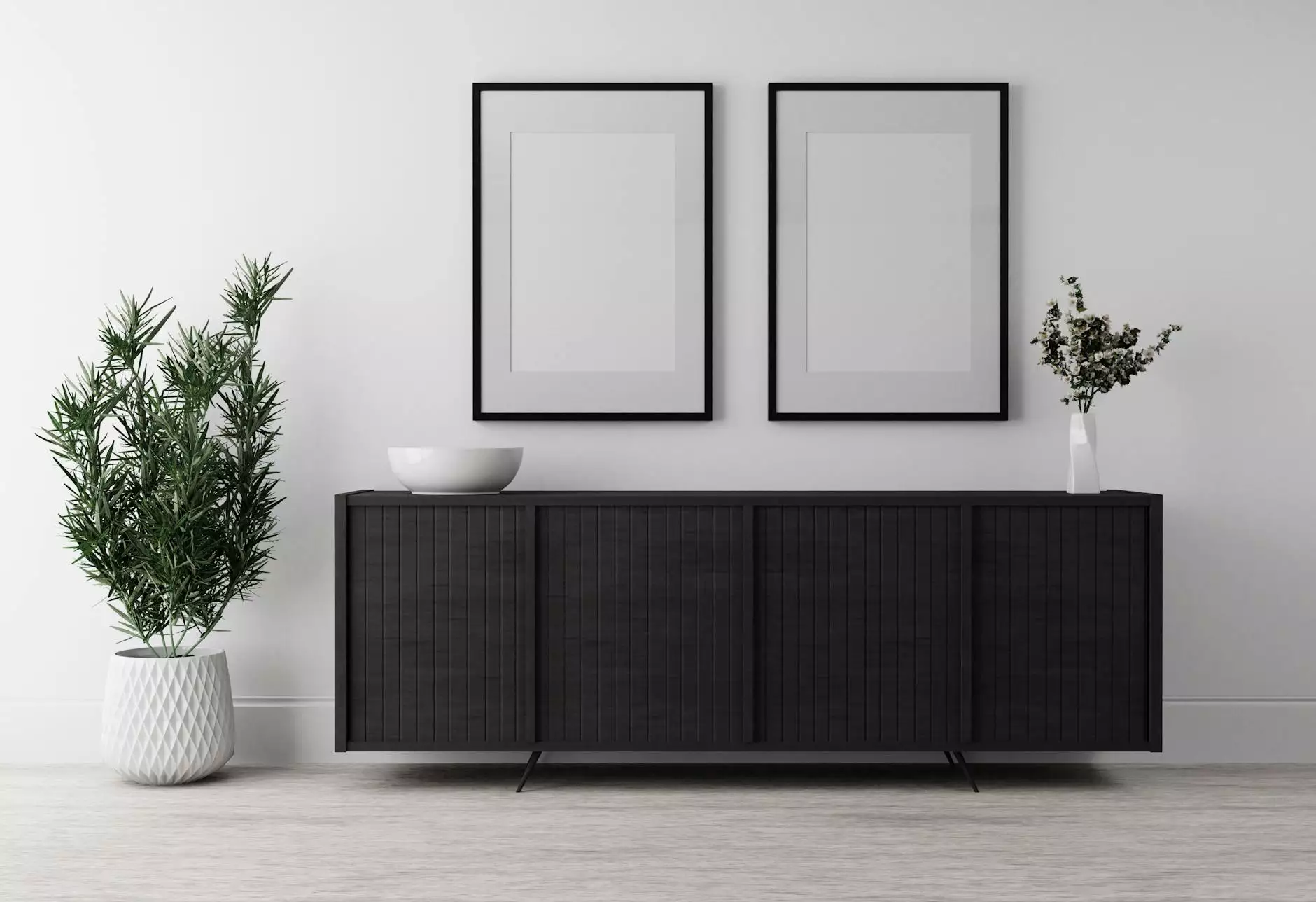
The world of manufacturing is evolving rapidly, with new technologies emerging to improve efficiency, precision, and quality in production processes. One such innovative technique is auto injection molding, a method that has captured the attention of the metal fabrication industry. This article delves deep into the mechanisms, benefits, and future prospects of auto injection molding, offering you a comprehensive understanding of its significance in modern manufacturing.
What is Auto Injection Molding?
Auto injection molding is a manufacturing process used to produce parts made from thermoplastic and thermosetting polymers. During this process, a material is heated until it becomes liquid, then injected into a mold under high pressure. Once the plastic cools and solidifies, it takes the shape of the mold, creating components with precise dimensions and intricate designs. This advanced technique is particularly useful in the production of metal components that need to be lightweight yet strong, a growing requirement in various industries.
The Process of Auto Injection Molding
The auto injection molding process can be broken down into several key stages:
- Material Selection: Choosing the right material is crucial. Common materials include nylon, polypropylene, and polystyrene, each offering unique properties suited for different applications.
- Heating: The selected material is heated in a barrel until it reaches a molten state, allowing it to flow easily into the mold.
- Injection: The molten material is injected into a precisely designed mold under high pressure. This ensures that even the tiniest details are replicated in the final product.
- Cooling: After injection, the mold is cooled, allowing the material to solidify. The cooling time can vary based on the material and part design.
- Demolding: Once sufficiently cooled, the mold opens and the finished part is removed. Additional finishing processes may follow to meet exact specifications.
Advantages of Auto Injection Molding
The introduction of auto injection molding has brought along numerous advantages that enhance manufacturing capabilities:
1. Efficiency and Speed
Auto injection molding is designed for high-volume production, allowing manufacturers to create thousands of parts in a single production run. The speed of the process minimizes lead times and increases overall productivity.
2. Precision and Quality
The technology ensures an extremely high level of precision, producing parts that meet strict tolerances. This is particularly important in industries such as automotive, aerospace, and electronics, where quality cannot be compromised.
3. Versatility
Different materials can be utilized in auto injection molding, making it adaptable for various applications. Manufacturers can experiment with composites and additives to enhance material properties based on specific project needs.
4. Reduced Waste
The process is highly efficient in material usage. Unlike traditional machining, which often results in a significant amount of waste, auto injection molding minimizes leftover material, leading to more sustainable manufacturing practices.
Applications of Auto Injection Molding in Metal Fabrication
The applications of auto injection molding are widespread, particularly in the metal fabrication sector. Here are a few notable uses:
- Automotive Parts: Auto injection molding is extensively used to create components such as dashboards, casings, and housings that require a combination of strength and lightweight properties.
- Aerospace Components: The aerospace industry benefits from the precision and performance characteristics of parts produced through injection molding. Components must meet rigorous safety and performance standards, making this technology ideal.
- Consumer Electronics: Products like smartphones and tablets use injection-molded components to house sensitive electronic parts. The design freedom allows for sleek, functional products.
- Medical Devices: The medical field relies on auto injection molding for the production of components that require high precision and adherence to strict regulatory standards.
Future Trends in Auto Injection Molding
As technology advances, the future of auto injection molding looks promising. Several emerging trends are likely to shape the landscape:
1. Increased Automation
Manufacturers are increasingly adopting automation technologies to streamline the auto injection molding process. Innovative robotics and AI solutions can enhance efficiency and reduce human error.
2. Sustainable Practices
The focus on sustainability is pushing manufacturers to explore biodegradable and recyclable materials for injection molding. The industry is actively seeking solutions to reduce its carbon footprint and improve environmental impact.
3. Advanced Materials
Research into advanced composites and smart materials is opening new avenues for auto injection molding. These materials can provide enhanced durability, strength, and functionality, catering to the evolving demands of various industries.
4. Customization and 3D Printing Integration
The integration of 3D printing technology with injection molding processes allows for rapid prototyping and customization. This hybrid approach is becoming increasingly popular, enabling manufacturers to meet the specific needs of clients more effectively.
Conclusion
Auto injection molding represents a transformative force in the metal fabrication sector, providing unrivaled efficiency, quality, and versatility. As manufacturers continue to embrace this technology, we can expect it to play an even more significant role in future production methods. Companies like DeepMould.net are at the forefront of this revolution, leveraging innovative techniques to meet the diverse needs of their clients. By understanding and harnessing the power of auto injection molding, businesses can not only improve their manufacturing processes but also enhance their competitive edge in an increasingly challenging marketplace.