Precision Plastic Parts: The Backbone of Metal Fabrication
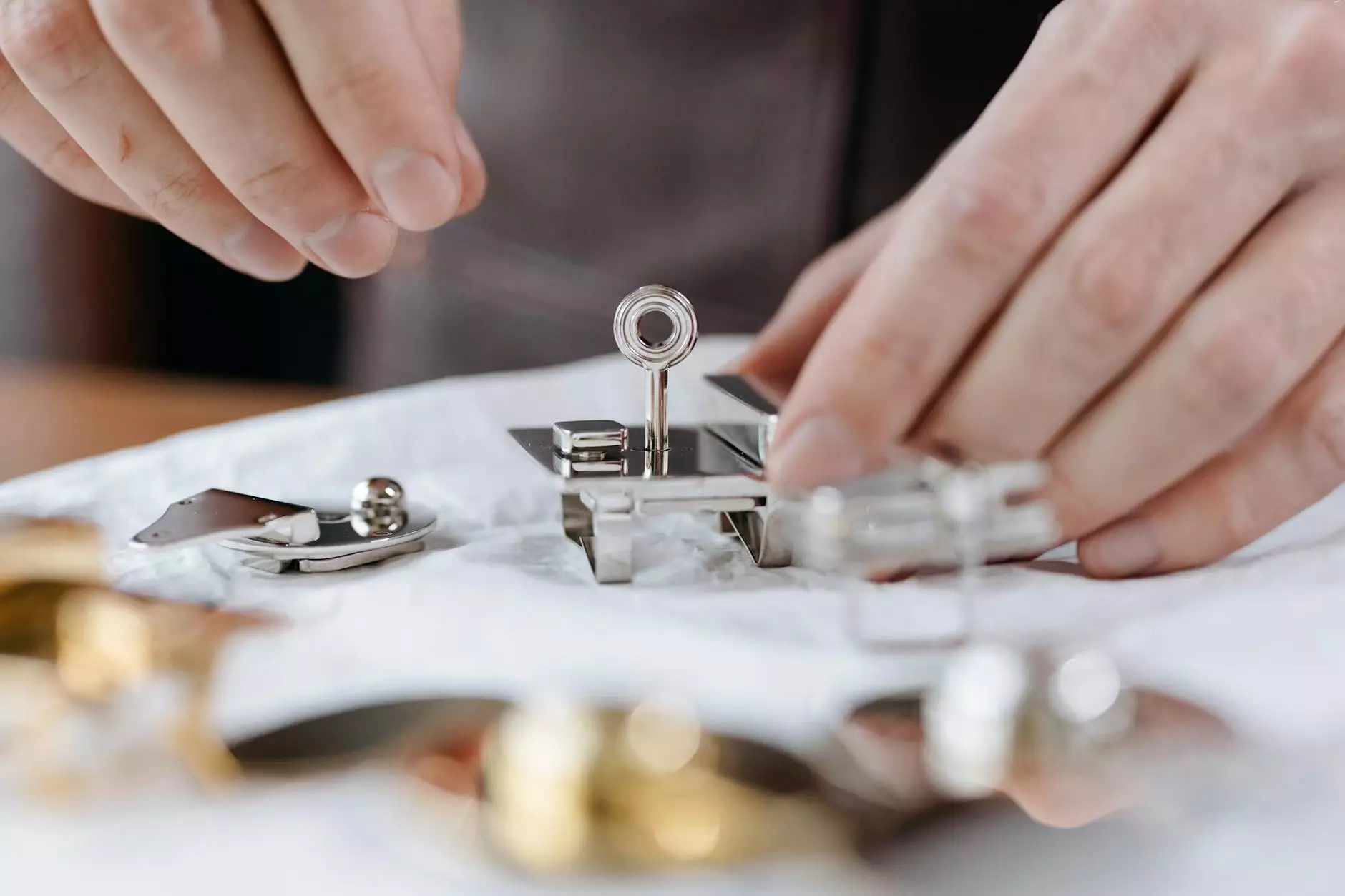
In the rapidly evolving landscape of manufacturing, particularly within the metal fabricators sector, the significance of precision plastic parts cannot be overstated. These components are essential for enhancing the efficiency, accuracy, and performance of various applications in the metalworking industry. This article seeks to explore the intricate world of precision plastic parts and their pivotal role in enriching the capabilities of metal fabrication.
The Importance of Precision in Manufacturing
Manufacturing precision is a vital element that directly influences the quality and reliability of the end product. Precision plastic parts play a crucial role in this aspect for several reasons:
- Quality Assurance: Precision parts facilitate consistency, reducing the likelihood of defects and enhancing product durability.
- Performance Optimization: They contribute significantly to the overall performance by ensuring that all components fit together seamlessly.
- Cost Efficiency: High-precision parts can minimize material wastage and labor costs, leading to better overall profitability.
Applications of Precision Plastic Parts in Metal Fabrication
The applications of precision plastic parts in metal fabrication are diverse and multifaceted. Here are some of the primary applications:
1. Jigs and Fixtures
Jigs and fixtures are essential tools used to hold and support workpieces during manufacturing processes. The incorporation of precision plastic parts into these tools enhances accuracy and repeatability. They are often lighter than their metal counterparts, making handling easier without compromising strength or stability.
2. Gaskets and Seals
In many metal fabrication applications, gaskets and seals made from precision-engineered plastics provide essential functions. They prevent leakage, resist harsh chemicals, and remain stable under varying temperatures, thus playing a key role in ensuring operational integrity.
3. Insulators
Electrical insulation is critical in many metal fabrication processes. Precision plastic parts serve as excellent insulators, providing safety and efficiency in electrical applications. Their durability and resistance to thermal deformation make them ideal for high-performance environments.
4. Component Housing
The housing of electronic components often utilizes precision plastic parts to offer protection and structural support. This is particularly important in environments subject to vibration or mechanical stress, where metal housings could fail more readily.
Production Techniques for Precision Plastic Parts
To achieve the high degree of accuracy and reliability that precision plastic parts demand, several advanced production techniques are employed, including:
1. Injection Molding
Injection molding is the most prevalent technique used to produce precision plastic parts. This method involves injecting molten plastic into a mold, where it cools and solidifies into the desired shape. The precision of this technique allows for complex geometries and tight tolerances.
2. CNC Machining
CNC machining offers exceptional precision and versatility. It involves the use of computer-controlled machines to cut and shape plastic parts into precise specifications. This method is particularly beneficial for low-volume production where customized parts are required.
3. 3D Printing
3D printing technology has revolutionized the manufacturing industry, allowing for rapid prototyping and production of complex shapes that were previously difficult or impossible to achieve. The ability to fabricate precision plastic parts on-demand reduces lead times and enhances design flexibility.
Benefits of Using Precision Plastic Parts in Metal Fabrication
The integration of precision plastic parts into metal fabrication processes offers several benefits:
- Lightweight: Plastic parts significantly reduce the overall weight of assemblies, which can lead to lower shipping costs and easier handling.
- Corrosion Resistance: Unlike metals, plastics do not corrode, making them ideal for applications in hostile environments.
- Customizability: Plastics can be easily molded into intricate shapes and can be colored or marked as needed to fit specific project requirements.
- Lower Costs: In many cases, plastic parts can be produced at a lower cost than their metal counterparts, particularly when using high-volume production techniques such as injection molding.
Challenges in Utilizing Precision Plastic Parts
While there are numerous advantages to employing precision plastic parts in metal fabrication, there are also challenges that need to be addressed:
1. Temperature Sensitivity
Many plastics have limitations regarding temperature. When used in high-temperature applications, they may deform or lose structural integrity. Understanding the material properties is crucial for selecting the right plastic for the application.
2. Mechanical Properties
While plastics have many advantages, they may not always offer the same strength and stiffness as metals. This limitation can affect how and where precision plastic parts are utilized within a metal fabricator’s workflow.
3. Environmental Considerations
With growing concerns about sustainability, the environmental impact of plastic production and disposal cannot be ignored. Manufacturers are encouraged to use recycled plastics or develop biodegradable alternatives whenever possible to minimize their ecological footprint.
Future Trends in Precision Plastic Parts
The landscape of precision plastic parts is constantly evolving. Here are some emerging trends that are likely to shape the future of the industry:
1. Automation and Smart Manufacturing
The integration of automation in the manufacturing of plastic parts is expected to improve efficiency and reduce costs. Smart manufacturing technologies, like IoT and AI, will likely be applied to monitor production processes and improve quality control.
2. Advanced Materials
Research into new materials is ongoing, with bio-based and high-performance plastics gaining traction in various applications. Innovations such as self-healing plastics or those with enhanced thermal properties will expand the range of possible uses.
3. Sustainable Practices
Sustainability will continue to be a critical concern, leading to increased demand for recycled and eco-friendly materials. Manufacturers will need to adopt greener production practices and contribute to a circular economy.
Conclusion
The role of precision plastic parts in the metal fabrication industry is significant and far-reaching. From enhancing operational efficiency to enabling the production of complex geometries, these components contribute to the overall quality and performance of manufactured goods. As the industry evolves, embracing emerging trends and technologies will be essential for manufacturers looking to maintain a competitive edge.
At deepmould.net, we understand the intricate relationship between precision plastic parts and metal fabrication. Our expertise and commitment to quality help businesses thrive in today's fast-paced manufacturing environment. Whether you require precision parts for jigs, fixtures, gaskets, or other applications, we stand ready to assist you with tailored solutions that drive success.